Vacuum assisting pumping
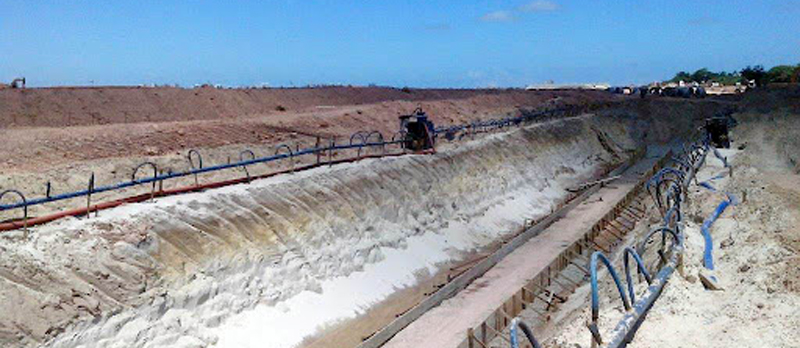
Vacuum-Assisted Pumping is a highly efficient method that enhances fluid movement by using a vacuum pump to remove air from the suction line, ensuring continuous and reliable operation. This technique is essential in applications such as dewatering, mining, and wastewater management, where maintaining prime is critical for performance. By preventing air blockages and enabling faster priming, vacuum-assisted pumps improve efficiency, reduce downtime, and extend equipment lifespan, making them ideal for demanding industrial environments.
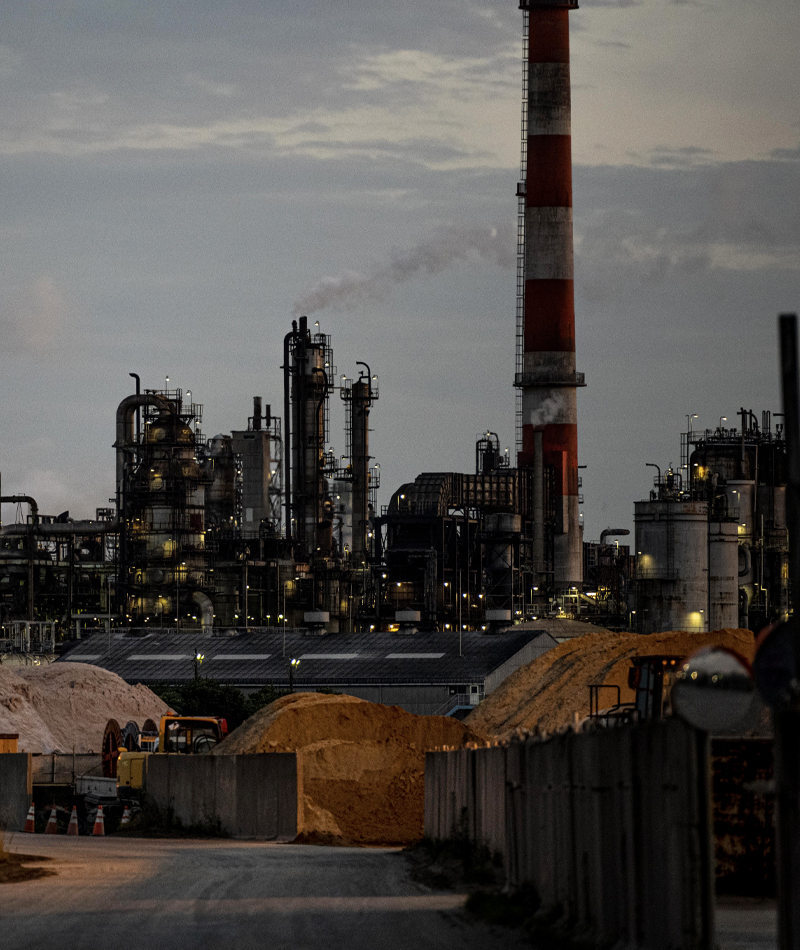
Suction of field pumps
The use of vacuum in field pumps is crucial to starting the pumping process, especially when working with centrifugal pumps and others that depend on priming to function properly. Let’s understand how vacuum helps in this process:
Pumping Start Problem
Suction Lift: When the water source is below the pump, water needs to be pulled up to the pump. This creates the need to remove air from the suction line to allow water to enter and fill the pump.
Air in the Suction Line: The presence of air prevents the pump from operating, since centrifugal pumps do not have the ability to operate on air alone.
Vacuum Solution
Vacuum Creation: A vacuum system removes air from the piping, creating a vacuum zone that allows atmospheric pressure to push water into the suction line and the pump.
Pump Filling with Water: By evacuating air, the vacuum ensures that the pump is filled with water before it starts operating. This is essential for lubricating and cooling the pump during operation.
Advantages of Using Vacuum
Efficiency: The use of vacuum priming systems makes the start-up process faster and more automatic, reducing the need for manual intervention and preparation time.
Reliability: These systems help maintain the pump prime, even in adverse conditions, preventing pumping failures.
Time Saving and Effort Reduction: The use of automatic vacuum systems minimizes the need for constant supervision, allowing field operations to be optimized.
-The use of vacuum is therefore an effective technique for ensuring that field pumps start and maintain their operation safely and efficiently, even in the most challenging conditions.
Lowering the water table
Importance of Vacuum in Groundwater Lowering Systems with Pipelines
Water table lowering is an essential technique in many engineering and construction projects, particularly when the groundwater level needs to be controlled to prepare foundations or perform excavations. The use of pipelines is one of the most common approaches, and vacuum plays a critical role in this process. Let’s explore the importance of vacuum in the efficiency of these systems:
Groundwater Related Issues
Flooded Areas: Before construction begins, it is crucial to remove excess groundwater to provide a dry and stable environment.
Structural Support: Excess water can interfere with the stability of structures, increasing the risk of collapse or subsidence.
Use of Vacuum Pipelines
Implementation: Pipelines are small tubes driven into the ground that allow the extraction of groundwater.
Vacuum Function: Applying vacuum to the nozzles increases the differential pressure, allowing water to be effectively pulled up from the ground, where it can be discharged or redirected.
Vacuum System Benefits
Efficient Water Removal: Vacuum speeds up water removal by reducing pressure in the collection zone, facilitating the continuous and efficient flow of water out of the nozzle system.
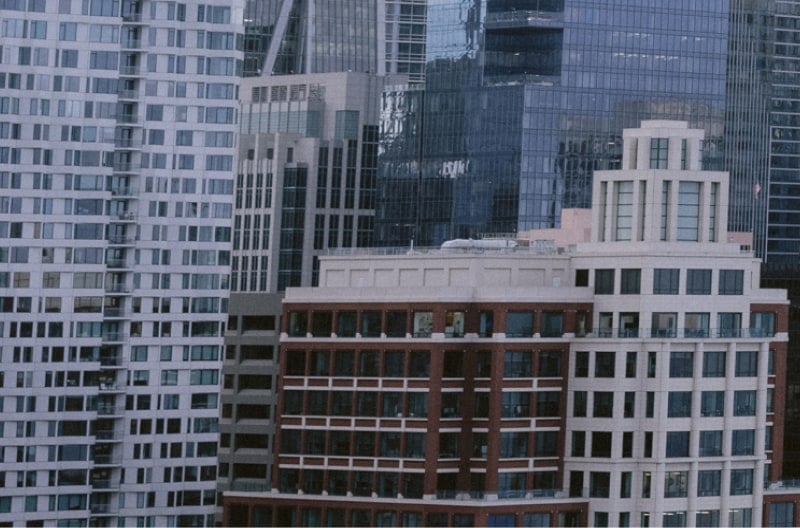
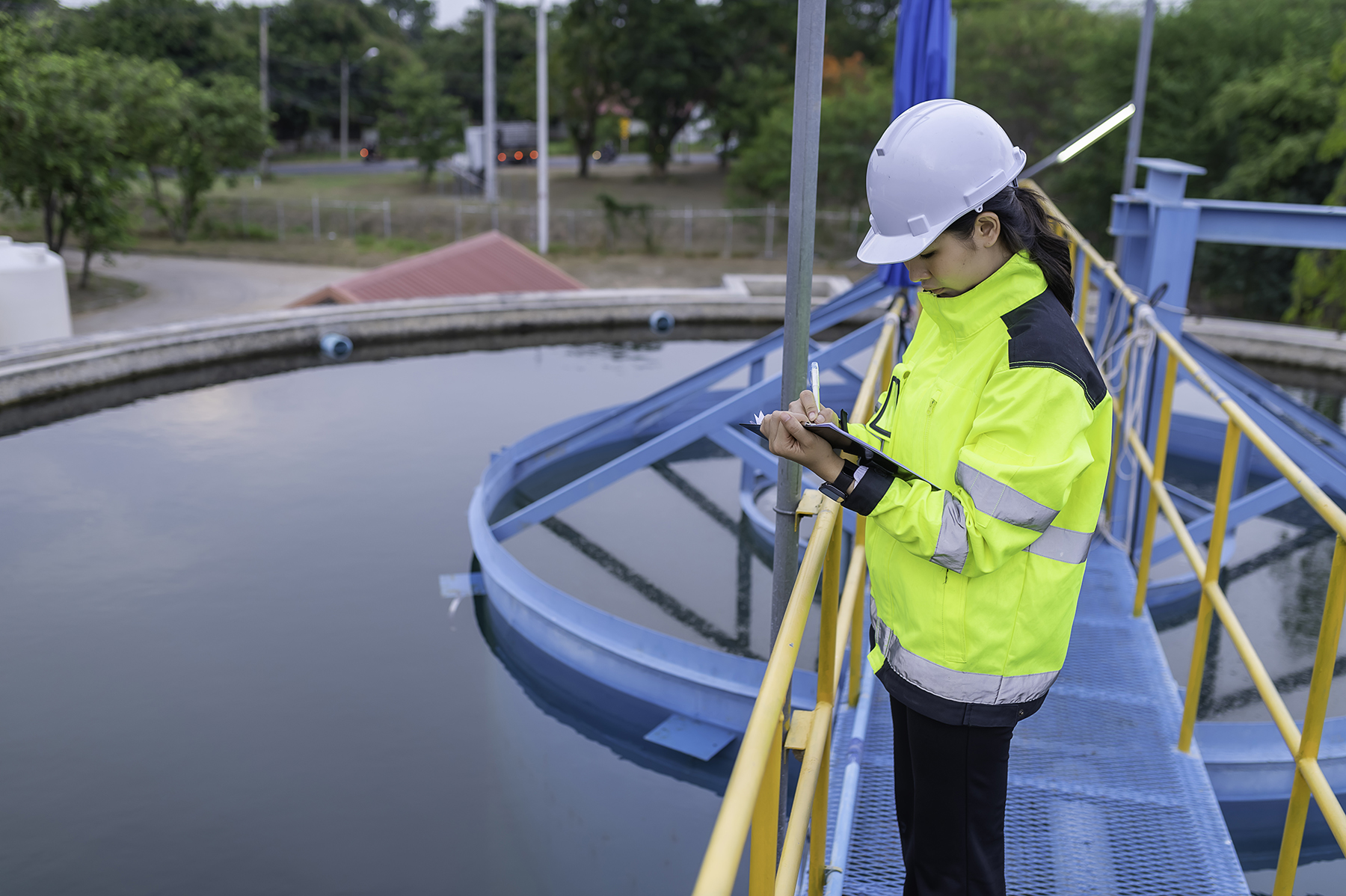
Precise Water Table Control: By regulating the vacuum level, operators can precisely control the groundwater level, quickly adapting to changes in soil conditions or job requirements.
Increased Soil Stability: Efficient removal of excess water improves soil stability, making construction areas safer for work and for the structures being erected.
Additional Benefits
Reduced Manual Intervention: Vacuum systems automate the extraction process, reducing the need for constant manual intervention and allowing the focus to other job activities.
Versatility: Can be used in a variety of soil types, including those with a high propensity for water accumulation.
Energy Efficiency: Modern vacuum systems are designed to operate in an energy-efficient manner, minimizing environmental impact.
In short, vacuum is essential to optimizing efficiency and control in point-based groundwater lowering systems, ensuring that subsurface conditions are effectively treated to support safe and sustainable construction.
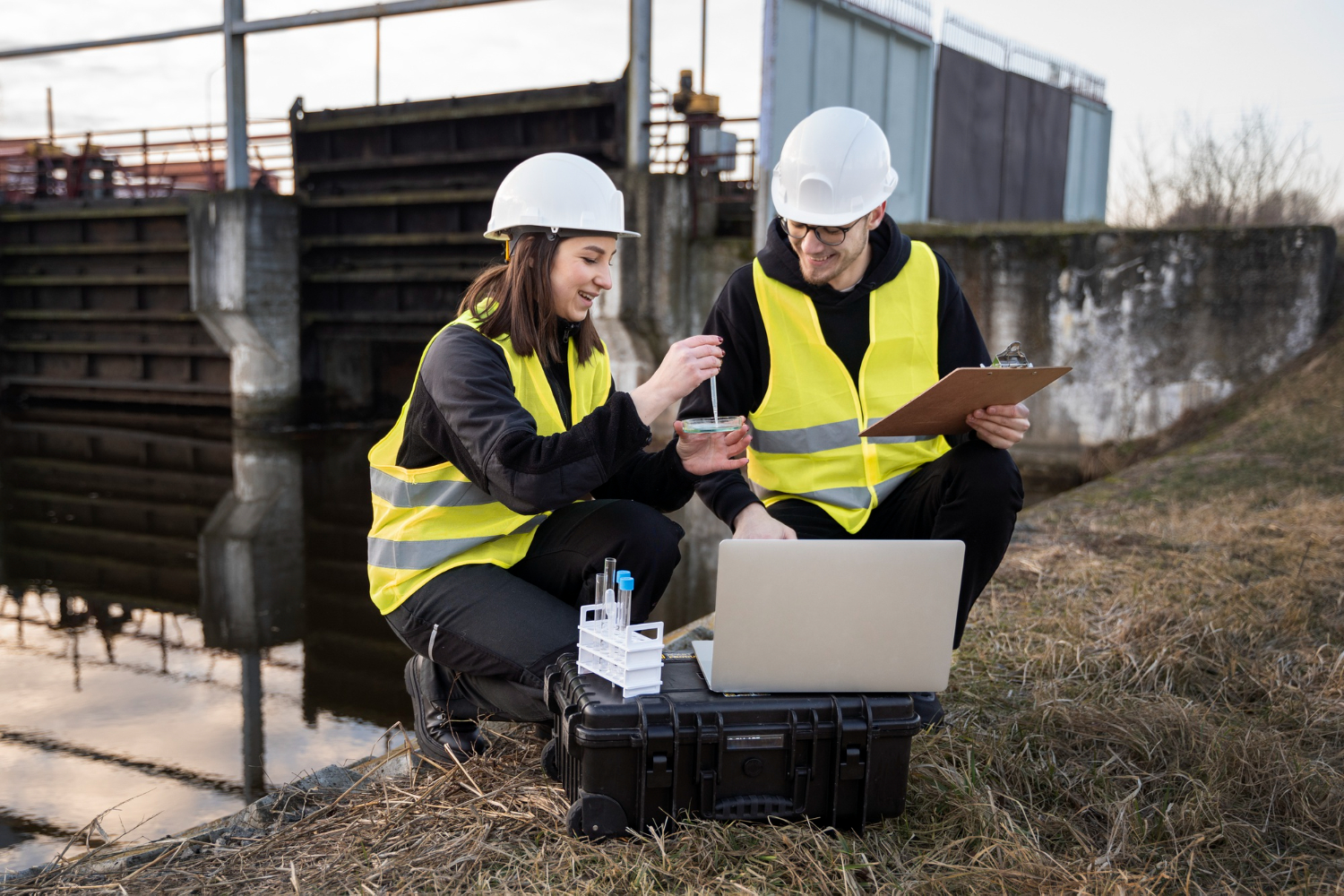
New facilities
Comparison between Conventional and Vacuum Priming Systems for Water Collection
When considering water collection in a facility where there is a significant difference in height between the river level and the pump, it is crucial to ensure that the suction line is always full to avoid pumping failures. Let’s compare the conventional method of using a foot valve with the vacuum priming system.
Conventional System with Foot Valve
Operation
Foot Valve: Installed at the bottom of the suction line, the valve prevents water from returning to the source, keeping the pipe full when the pump is not in operation.
Initial Filling: Before the first operation, it is necessary to manually fill the suction line to remove air.
Advantages
Simplicity of Installation: The technology is well understood and widely used, which facilitates installation and maintenance.
Initial Cost:Generally, the installation cost can be lower due to the lesser complexity of the components.
Disadvantages
Foot Valve Dependency: Any valve failure, such as leaks or blockages due to debris, can result in loss of prime, requiring frequent maintenance.
Manual Priming: The need to manually fill the line adds labor and time costs, especially in large installations.
Variable Efficiency: Less efficient when dealing with frequent changes in water level or operating conditions.
Vacuum Priming System
Operation
Vacuum System: Utilizes a vacuum pump to automatically remove air from the suction line, ensuring that the pipeline is always filled with water before and during operation.
Automation: Eliminates the need for manual intervention for initial priming.
Advantages
Automatic Operation: Reduces the need for manual intervention and allows for quick responses to changing conditions.
Increased Reliability: Reduced risk of loss of prime, as the system automatically adjusts to remove air and maintain efficiency.
Operational Efficiency: Improves energy efficiency and reduces downtime.
Disadvantages
Initial Cost: May be more expensive initially due to advanced technology and additional components.
Technical Complexity: Requires technical expertise for proper installation and maintenance.
In summary, while the conventional foot valve system is simple and familiar, the vacuum priming system offers greater reliability and operational efficiency under contemporary conditions, justifying its higher initial cost in many situations.
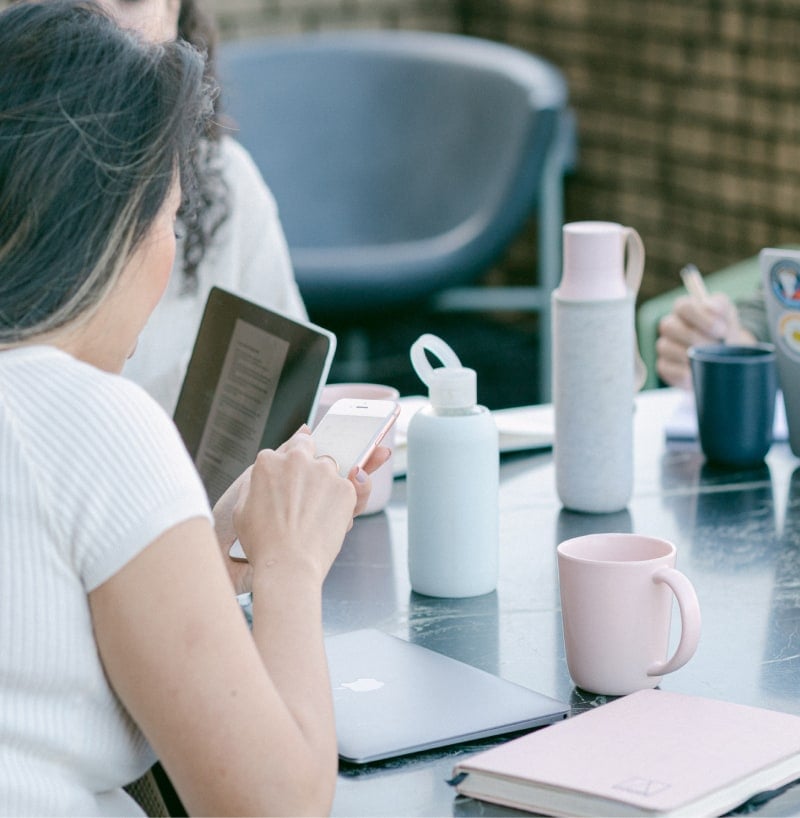
New markets and clients
Potential New Markets for 50 CFM Diaphragm Vacuum Pumps
Diaphragm vacuum pumps are known for their efficiency, low maintenance and oil-free operation, making them ideal for a variety of applications. Let’s explore some potential markets where these pumps can be implemented beyond priming systems:
1. Food Industry
Processing and Packaging: Can be used in processes that require controlled air handling and gassing, such as vacuum packaging and modified atmosphere filling.
Degassing: Ideal for removing unwanted gases from food liquids.
2. Chemical Industry
Transfer of Sensitive Chemicals: Diaphragm pumps can be used in chemical transfer, where product integrity and purity are critical due to their oil-free operation.
Filtration Systems: Used to create vacuum in filtration systems, improving process efficiency.
3. Laboratories and Research
Scientific Applications: Widely used in laboratories for applications such as chromatography, vacuum drying, and rotary evaporation.
Gas Analysis Equipment: Suitable for moving gas samples in analytical equipment.
4. Medical Industry
Aspiration Equipment: Can be used in medical suction machines, where a clean and controlled vacuum is required.
Sterilization Systems: Applications in sterilization processes that require efficient air removal.
5. Water and Wastewater Treatment
Air Removal: Used in water treatment systems to remove air from pipes and improve the flow of liquids.
Leak Testing: Can be used for leak detection and preventive maintenance in pipes and closed systems.
6. Automation and Industrial Processes
Material Handling Systems: Can be implemented in robotic handling systems that require suction to move parts and components.
Electronics Manufacturing: Used in the manufacturing of electronic components, where precision and cleanliness are essential.
Considerations for Expansion
Market Research: Conduct a detailed market analysis to understand the specific needs and regulations in each industry.
Industry Partnerships: Establish strategic alliances with companies in the mentioned industries to facilitate market entry.
Product Innovation and Development: Adapt and customize the pump to the specific needs of new markets in order to maximize its performance.
Exploring these new markets can not only expand the use of 50 CFM diaphragm vacuum pumps, but also open up new business and innovation opportunities for BRPumpParts.